-
Capabilities
Hydro’s broad capabilities are backed by expertise, years of committed service to our customers, and distinguished by a unique culture of dedication, unparalleled in our industry. Repairing and babbitting bearings are both a science and an art, where technical capability and skilled craftsmanship work hand-in-hand
Babbitt Bearing Repair
& Manufacturing
Our bearing services cover a large range of sizes, applications, and metallurgy, but have one thing in common; a commitment to quality that allows you to feel confident in the continued safe, reliable operation of your units.
From our rigorous dimensional analysis and strict acceptance criteria to our final NDE inspection, Hydro Richards’ attention to detail and exacting processes guarantee a superior product.
Our extensive experience with babbitt bearings allows us to support our customers in more than just manufacturing and refurbishment. For bearings with poor reliability, we provide root cause analysis of the underlying problem and provide targeted solutions.
Hydro Richards has the capability to service bearings up to 100” in diameter and 72” wide, and can refurbish and manufacture new bearings in a variety of designs including:
- Plain & flanged journal bearings
- Tilting pad journal bearings
- Radial thrust bearings
- Axial tilting pad
- Thrust bearings
- Guide bearings
- Trunnion bearings
- Marine bearings
Precision Machining
& Fabrication
Hydro Richards fabricates a wide range of industrial equipment. All equipment manufactured at our facility goes through a thorough inspection process, extensive process control procedures, stringent acceptance criteria, engineering support, and review–all carried out by an experienced workforce dedicated to providing a quality product.
Custom fabrication provides significant benefits over “off-the-shelf” products. Beyond flexibility in shape and size, custom fabrication provides a wider variety of component materials and adherence to improved tolerances.
Our precision metal fabrication and machining services include design, construction, testing, finishing, assembly, and installation. We have significant experience in various industries, including food processing, marine, mining, pump bases, and elevator equipment.
The following services are available on a 7 day, 24-hour basis:
- Shaft turning to 20" diameter, (34" gap) x 120" long
- Vertical turning on a 60"
- Milling 80" x 90" x 42" high
- Shaft cylindrical grinding between centers to 130" long
- Internal cylindrical grinding to Ø36” diameter x 12" long
- Surface grinding 8” x 25” x 13” long
- Line and positional boring
- Weld repairs to carbon steel, austenitic and duplex stainless steels
- Post weld heat treatment
- CNC coordinate measuring
- Dye penetrant examination
Fusion Welding &
Engineered Solutions
Hydro’s knowledgeable team is supported by the most comprehensive repair capabilities in the world. Expertise in pump design, mechanics, and repair define Hydro’s unmatched capabilities.
Hydro Richards provides fusion welding technology for remanufactured and OEM components for high-volume surfacing, complex geometries, irregularly-shaped parts, multidimensional profiles, and threaded areas. Advantages of laser welding include:
- Fusion welding of stellite and colmonoy hard surfacing
- Selective hardness ranges
- Various levels of corrosion resistance
- Matching substrate chemistry
- Minimal inter-metallic dilution
- Low heat input
- Low thermal distortion
- Narrow heat-affected zone
Case Studies & Customer Success Stories
Quality work begins with a quality shop. Hydro Richards is fully-equipped to handle all of your rotating equipment needs. Virtually all repair processes can be handled in-house, resulting in greater efficiency and faster turnaround for your pump repair project.
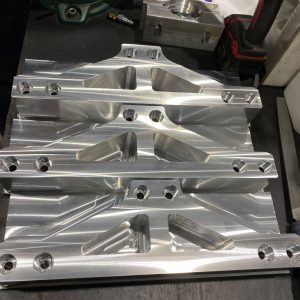
Structural braces for large industrial equipment
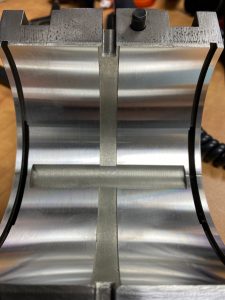
Journal bearing design for a centrifugal pump
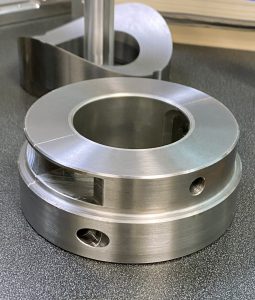
Journal bearing for a centrifugal pump
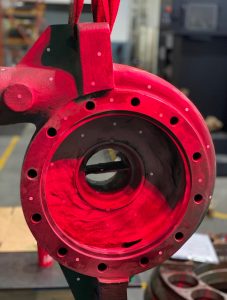
Dots utilized during the reverse engineering scanning process
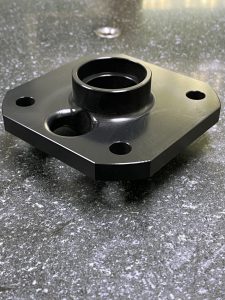
Bearing support
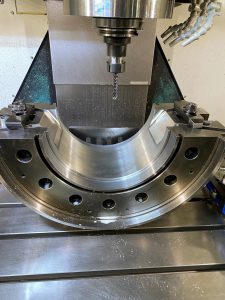
Babbitted bearing guide in the process of machining
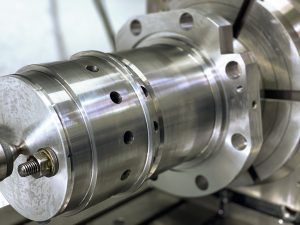
Precision machined component for a nuclear power plant
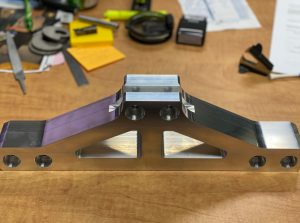
Structural brace for large industrial equipment
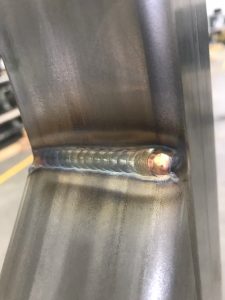
Industrial fabrication of a manufacturing stand for a small business of chocolate makers
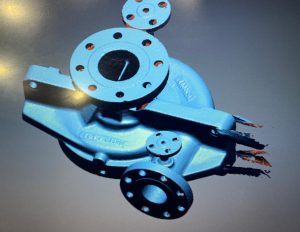
Software screenshot of the 3D modeling process of a centrifugal pump casing
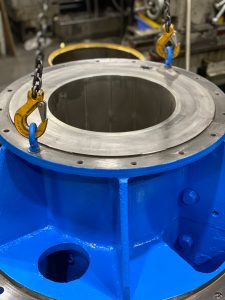
Finished and machined guide bearing
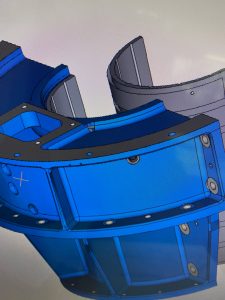
Guide bearing 3D model
Parts Solutions
for the Pump Aftermarket
Hydro Richards has the capability and experience to reverse engineer and replicate parts for a wide range of equipment. Using our Creaform handheld 3D Scanner, we can efficiently scan a part and digitize the dimensional data. The digital model created is used to machine the new component, which is then scanned using the same technology to confirm adherence to the original part’s dimensions.
Reverse engineering is an important tool for supplying quality parts in circumstances where long lead times or quality issues with original equipment manufacturers have proven burdensome. It is also an essential service for sourcing parts when equipment is obsolete and parts can no longer be easily procured.
Often times, the material stated on a bill of materials varies slightly from the actual material used in manufacturing a part. As part of our reverse engineering or repair processes, we provide material testing and analysis to verify component material.
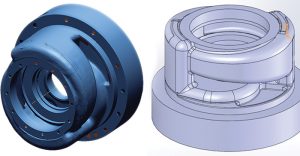
- Design modification from existing components
- Advanced Class-A surface modeling and Class-B surfacing
- Parametric 3D modeling in generic or native file formats
- Data preparation for digital simulation
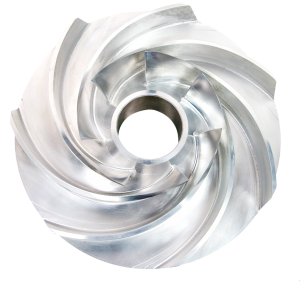